SMED
Een snelle omstelling waardoor de OEE verbetertWat is SMED en waarom doen we het?
SMED staat voor Single Minute Exchange of Dies. Het is een Lean-tool waarmee omsteltijden drastisch gereduceerd worden. De grondlegger is Shingeo Shingo, een Japanse engineer die bij Toyota het Toyota Production System heeft ontwikkeld. Basis daarvan waren Poka Yoke en SMED.
Deze laatste wordt met name toegepast in productieomgevingen maar het kan ook zinvol zijn eens te kijken naar omstellingen in dienstverlening. Als je snel in staat bent om te stellen dan wordt het productieproces flexibeler en kan sneller op klantvraag geproduceerd worden. Het effect hiervan is dat de productiecapaciteit verhoogd wordt, ofwel de OEE verbeterd. En het effect is ook dat je minder eindvoorraad hoeft te houden omdat je sneller kan omstellen.
In dienstverlening is een omstelling vaak verborgen, maar ze zijn er wel degelijk. Denk maar eens aan een telefoontje dat je krijgt van een klant terwijl je een offerte aan het schrijven bent. Je gaat uit het éne proces (offerte schrijven) en komt in het andere proces (de klant te woord staan).
Dit kost even tijd. En om terug te gaan, heb je ook weer tijd nodig. Het is sneller als je de offerte gelijk afmaakt en daarna de klant te woord staat. Maar de vraag is of de klant daar blij van wordt natuurlijk. Ook heb je te maken met een omstelling, als je mail-alert aan staat terwijl je een mail aan het beantwoorden bent. Je krijgt een pop-up van een nieuwe mail en wordt met je aandacht toegetrokken naar de binnenkomende mail. Als je hier vervolgens naar gaat kijken, heb je je omstelling al te pakken. Dit kost tijd en is niet zo effectief. Er zijn inmiddels mail-trainingen om hiermee om te gaan, maar in feite hebben we het dan over omsteltijdreductie. Zie hiervoor ook ons artikel over time-boxen.
Maar terug naar de productie omgeving waar SMED vandaan komt.
Hoe wordt SMED toegepast en hoe werkt het?
Wanneer we SMED toepassen, gaan we kijken naar de omstelling zelf en observeren we deze een aantal keer. We meten tegelijkertijd ook hoelang de processtappen duren. Hieruit komt een waardestroom-analyse of procesplaat van de omstelling zelf. Vaak is het daarna nodig om nog meer metingen te doen van de verschillende processtappen. In feite zijn we nu een DMAIC aan het doorlopen ofwel een Define, Measure, Analyse, Improve en Control.
Na of tijdens het uitvoeren van de meting gaan we de omstelling analyseren. We kijken naar de verschillende fases en kijken naar de wachttijden en de dingen die slimmer kunnen. Samen met de mensen die de omstelling vaak doen, kijken we naar de resultaten. Vaak zijn er nu al Quick Wins te zien die opgepakt kunnen worden. Bijvoorbeeld het reduceren van wachttijden. Deze Quick Wins zijn vaak makkelijk op te pakken.
Vervolgens zien we dat er wat ingewikkeldere zaken zijn, die vaak door een slimme aanpak ook tot omsteltijdreductie leiden. We zien bijvoorbeeld dat we zaken in de voorbereiding kunnen doen terwijl de machine nog productie draait, in plaats van in de tijd dat de machine stil staat om om te stellen. We noemen dit van interne tijd (tijd binnen de omstelling) naar externe tijd gaan (tijd buiten de omstelling, dus de periode waarin er productie wordt gedraaid). In de implementatie gaan we deze oplossingen doorvoeren en vervolgens borgen. Laten we eens een voorbeeld bekijken.
Een voorbeeld is een SMED-traject in productie.
Een spuitgietbedrijf maakt plastic mallen om producten in te pakken. Ze hebben een grote vraag en inmiddels een vrij lange levertijd. De omstelling duurt hier zo’n 4 uur. Bij het meten van de omstelling zien we dat er verschillende fases zijn. Ook hebben we een tijdsmeting van deze fases gedaan:
- Voorbereiding, machine uit productie nemen: 14 minuten
- Uitbouw oude mal: 32 minuten
- Inbouw nieuwe mal: 64 minuten
- Stellen van de machine zodat de productie met het nieuwe product gedraaid kan worden: 65 min
- Vrijgave voor schoonmaak en wachten hierop: 21 min
- Schoonmaken: 25 min
- Vrijgave voor productie: 22 min
Te zien is dat de vrijgaven van de machine behoorlijk lang duren en de voorbereiding om tot uitbouw te komen ook. Totaal is dit 57 minuten. Ook zien we dat het schoonmaken vrij lang duurt. Door het schoonmaken te starten tijdens de laatste handelingen van het stellen, schuiven we twee zaken in elkaar en reduceren we al een deel schoonmaaktijd en de vrijgave voor schoonmaak. Ook de vrijgave voor productie reduceren we tot nul minuten doordat we de steller aanwezig laten zijn tot afronding schoonmaak. Verder kunnen we de voorbereiding deels doen terwijl de machine draait. We maken van interne tijd nu externe tijd.
In totaal reduceren we hierdoor de tijd al met 14 + 21 + 15 + 22 minuten = 72 minuten. Vervolgens gaan we de uit- en inbouw analyseren en besluiten we om dit met twee personen te doen die dit samen in een veel kortere tijd doen. Hierdoor wordt ook het stellen van de machine verkort. Bijkomend voordeel van met twee personen werken is dat mensen hierdoor van elkaar leren en een senior en junior samen kunnen werken.
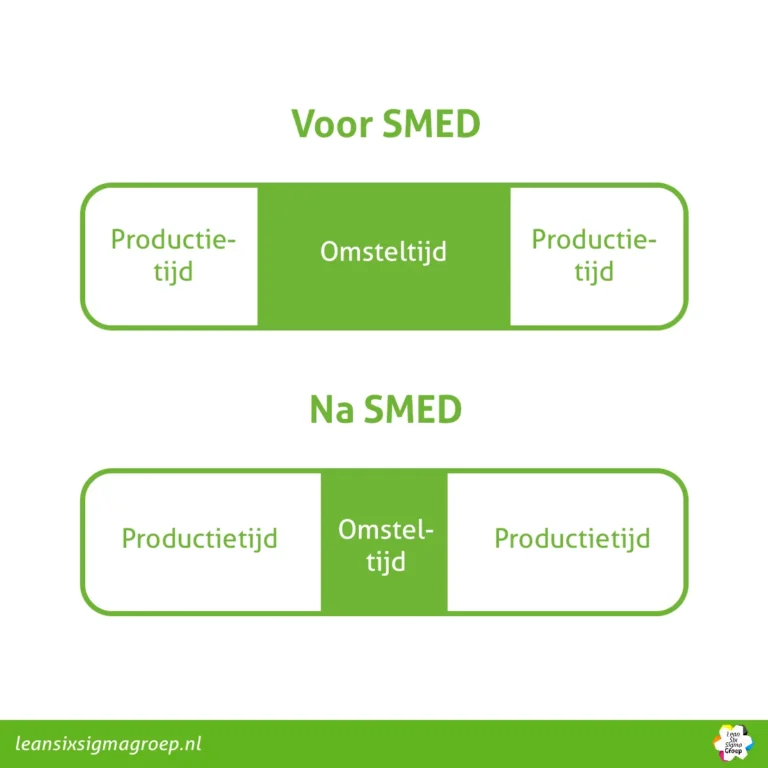
Door dit traject zijn we in staat om de omstelling naar 100 minuten te reduceren: een uur en 40 minuten. Hierdoor kan er veel meer productie gedraaid worden en gaat de OEE omhoog. Bovendien zijn er ideeën opgedaan om de omstelling in de toekomst nog slimmer te doen, hier worden tools voor ontwikkeld.
Samenvattend is SMED een mooie tool om flexibeler en effectiever te produceren
Wat we zien is dat Single Minute Exchange of Dies een mooie manier is om omsteltijden aanzienlijk te verlagen, waardoor in veel kleinere batches geproduceerd kan worden. Dit ligt aan de basis van het Lean-gedachtengoed en heeft veel meer effect dan je in eerste instantie misschien denkt. Dus… denk ook eens na over de omstellingen van jouw eigen proces en hoe je deze kunt verminderen.