What is Kaizen process?
Kaizen emerged as a concept in Japan following World War II. The Japanese word 改 (“kai”) means “change” and 善 (“zen”) means “good”. The philosophy was designed by Masaaki Imai. The Toyota production system is renowned for its Kaizen philosophy. In this approach, frontline workers are encouraged to halt their production line upon encountering a deviation by pulling an andon cord. They are then expected to collaborate with their supervisor to suggest and implement improvements aimed at resolving this deviation.
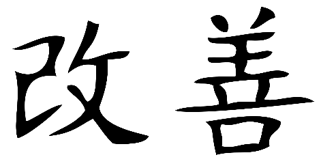
It is a daily activity with a purpose beyond improvement. It is also a process that, when done correctly, makes the workplace more humane: it eliminates hard work (both mental and physical) and it teaches people to see and eliminate waste in a process.
The core of the Kaizen method consists of 5 basic elements:
- Teamwork
- Personal discipline,
- Improved morale,
- Quality circles,
- Suggestions for improvement.
Kaizen event
A Kaizen event represents a project that spans from problem identification to the implementation of solutions, all within the span of a few days. The primary objectives are cost reduction, quality improvement, shortened delivery times, or enhanced customer satisfaction.
Conditions in a Kaizen-event:
- The problem must be urgent and have a limited scope and complexity.
- The employees involved must be 100% available during the Kaizen event.
- It is always with people from the process.
- Typically, it focuses on the process at the activity level.
- Look for creative solutions first before spending money.
- Ask as much as possible (5x why) to get to the root of causes.
- Implement good solutions, don’t keep looking for the perfect solution (keep pace).
- A plan is only good if it can be implemented and a plan is only successful if the success is assured.
After the project is completed, Kaizen can be used to achieve a continuous improvement culture.
Improvement cycle at a Kaizen event
A Kaizen event goes through 6 steps, which correspond to the DMAIC method. The roadmap from the improvement circle, in brief:
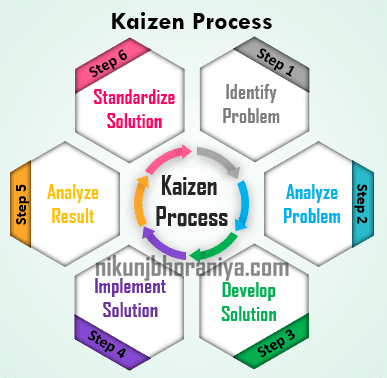
- Define the problem and the objective. What is the real problem? What is the objective? Formulate the goal as clearly as possible.
- Measure the facts. Go to the Gemba. Go and see in the actual workspace. Visualise the process with a value stream map. Collect data to clearly identify the problem.
- Analyse the facts. Brainstorm about the causes. Ask as many questions as possible (5x why). Make, for example, an Ishikawa diagram. Select the biggest causes of the problem.
- Generate improvements in the causes. Brainstorm improvements.
- Implement improvements. Rank the improvements. Create and implement an implementation plan.
- Check and secure. Verify that the problem has been solved. Record the solution. Write new ways of working and communicate them.
Kaizen and Lean
Lean focuses on eliminating waste. It is a working method that focuses on efficiency. It involves developing a flexible working environment that puts the customer first and eliminates waste as much as possible. Within the broad spectrum of Lean, there exists a range of techniques concentrated on process enhancement and waste elimination. Among these approaches is Kaizen, a notable component.
Kaizen takes a step beyond mere waste elimination; it revolves around the concept of continuous improvement. It involves the ongoing enhancement of your organization, leading to transformative changes. Consider Toyota’s factory as an example, showcasing how they employ Kaizen for continuous improvement: