What is Lean?
Maximum value for the customer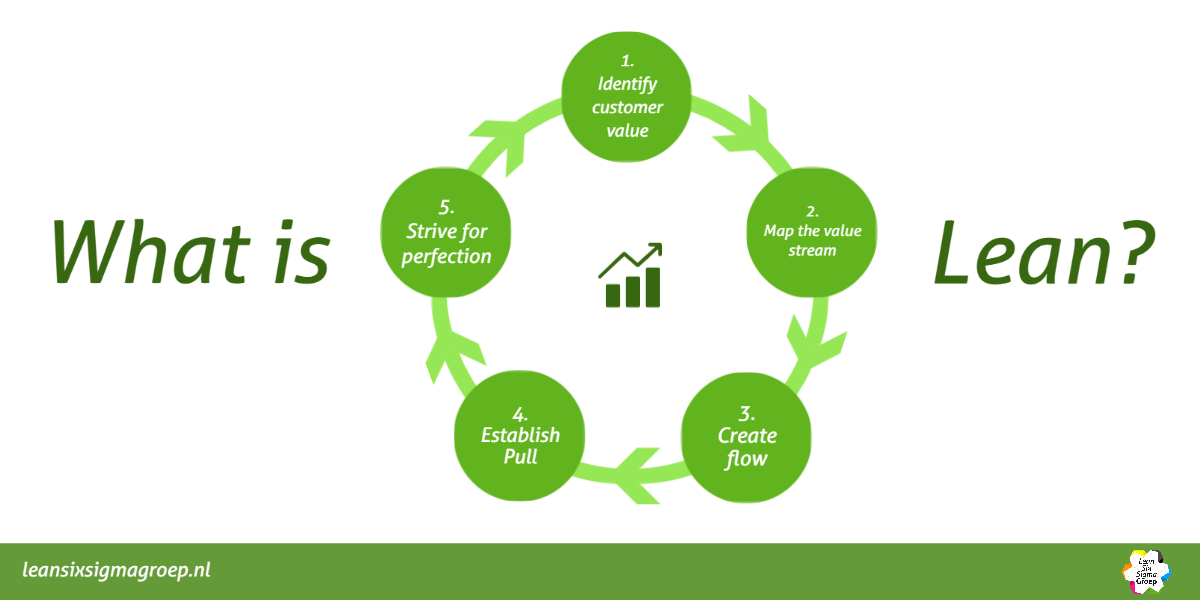
What is Lean? A simple question, right? But it is not that easy to answer that question. Literally the translation is “slim” and “without too many extras”, but that is fairly blunt. The term Lean was coined by Womack and Jones after visiting Toyota factories in Japan.
How did the term originate?
Henry Ford
The first person to really integrate a full production process was Henry Ford. In Highland Park, MI, Henry Ford designed his first ‘moving assembly line’ in 1913, revolutionizing the production process of his Ford Model-T. The problem with Ford’s system was not flow, rather it was his inability to provide variation. When the world wanted variation, Ford seemed to be getting lost.
Toyota
When Kiichiro Toyoda, Taiichi Ohno and others at Toyota looked at this situation in the 1930s, and more intensely shortly after World War II, they realized that a series of simple innovations could enable both continuity in the process flow and a wide range of product offerings. They have therefore revised Ford’s original thinking and invented the Toyota production system.
Womack en Jones
Womack and Jones were in Japan to unravel the secret of the successful Japanese management style. They recorded their discoveries in a book, “The machine that changed the world”, an outright bestseller. But no matter how successful the approach was, the managers at Toyota hadn’t even come up with a name for their systematic way of working. James Womack and Daniel Jones christened this “Lean” for lack of a better term.
What does Lean mean?
So “Lean” is not an abbreviation or acronym, it is not a creator name, it is not a pre-conceived term of a production system. But more important than the name, what does Lean mean?
- It is a management philosophy, a way of working and thinking to manage processes in companies.
- It’s a different way of looking at your processes that allows you to recognize and eliminate wastes.
- It is the most respectful way of dealing with employees and encouraging them to do the right things.
- It means that the customer indicates how your product or service best solves his problem and with that the customer in fact determines the underlying process.
- It is the stimulation of asking questions and perceiving without judgment, instead of immediately giving an answer, solution or judgment.
- It is a way of working. Work more fun, easier and more effective.
- It is also a communication method to deal with problems.
- It is striving for perfection for customer and company.
How does Lean work?
There are five steps from the Lean model that are important to make a process completely Lean:
- Who is the customer of the process and what does the customer want?
- What does the process look like? Mapping the process by, for example, a value stream map
- How can you bring the flow into the process? Which process steps provide added value? How are you going to add value?
- Where are the wastes and where is the flow lacking in the process?
- Striving for perfection and continuous improvement
The above Lean principles help to organize processes intelligently and continuously strive for improvement. We have listed these 5 basic principles from Lean Management in another article for you with more explanation.
Lean organization
“Just as a carpenter needs a vision of what to build … to get the full benefit of a hammer, Lean Thinkers need a vision before picking up our Lean tools. Thinking deeply about purpose, process, people is the key to doing this.”
Womack and Jones recommend thinking about three fundamental business issues that should guide the transformation of the entire organization. This is specifically for managers and executives who want to enter a Lean transformation:
Goal: What customer problems will the company solve to achieve its own goal of success?
Process: How does the organization assess each major value stream to ensure that each step is valuable, capable, available, sufficient, flexible, and that all steps are linked by flow, pull and leveling?
People: How can the organization ensure that in every important process, someone is responsible for continuously evaluating the value stream regarding business purpose and lean process? How can anyone who touches the value stream be actively involved in the correct operation and continuous improvement?
Lean and Six Sigma
“Lean is where customer and company come together in the best possible way” – Kim, Green Belt in training