Ishikawa Diagram
How to make Lean practical with an Ishikawa- or fishbone diagram? The term ‘ practical’ has a few synonyms, such as ‘ efficient ‘ , ‘convenient’ , ‘ applied’ and ‘ useful’ . Fortunately, Lean is also nice and practical, or in other words, you can use it in practice. You can apply Lean to many situations, both at work and at home.
The philosophy of Lean focuses on the added value for the customer. From a customer perspective, we look at how we can best design our processes. Incidentally, this is also a matter of just plain old common sense. You learn to actually live the Lean philosophy over the years.
Apply directly
The other side of Lean, the practical side, can actually be applied immediately.
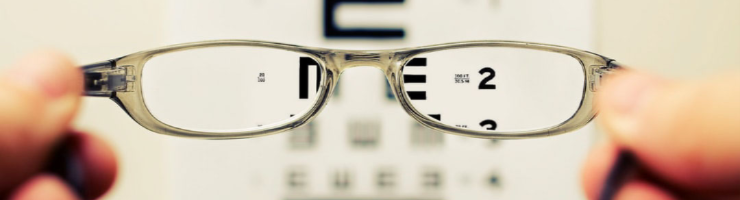
Put on your Lean glasses
- Use post it’s to describe the possible causes (brainstorming).
- Group the causes that belong together.
- Ask at every post-it by why this is a cause? Or, in other words, what other causes are behind it? Continuing to ask up to five times ensures that you get closer and closer to the actual source of the problem.
Of course, this does require some tact and practice. But you can learn that at Lean Six Sigma Groep and put it into practice under the guidance of one of our Black Belts. Do you also want to get started with Lean in practice and get results right away? Check out our training courses here.
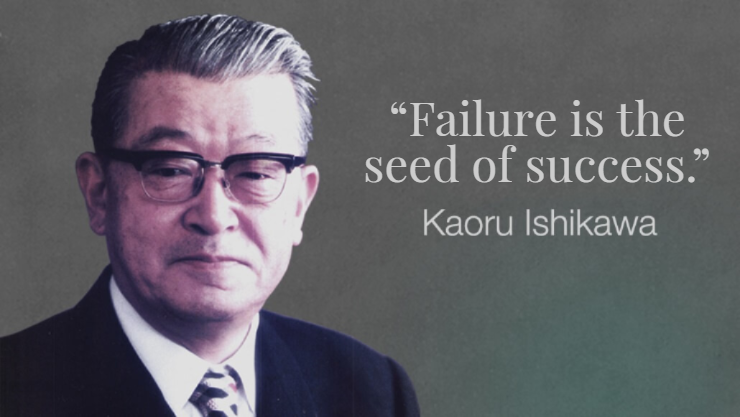
How does a Fishbone diagram works?
- The head of the fish is created by listing the problem in a statement format (see example).
- A horizontal arrow is then drawn across the page with an arrow pointing to the head, this acts as the backbone of the fish.
- It then identifies at least four overarching cause categories that may contribute to the problem. Some generic categories: man (people), methods, machines, materials, measurements, and mother nature. The overarching causes are drawn with arrows, off the spine, as branches, forming the first bones of the fish. About each overarching cause, team members brainstorm to gather additional information (in the form of underlying causes).
- With interrogation (5 x why), the most important causes are selected from all the collected ones. Ultimately, this leads to several root causes being detected.
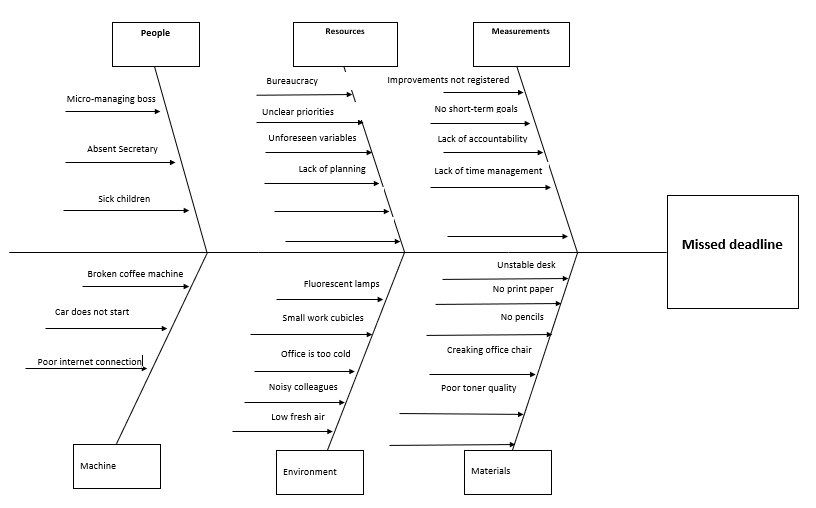
We have used the following six categories for the above fishbone diagram:
- Man: Everyone involved in the process.
- Methods: How is the process carried out and what requirements (rules, procedures, regulations, laws et cetera) are involved?
- Machines: Equipment needed to perform the task.
- Materials: All the materials and parts used to create the product.
- Measurements: Data generated from the process to analyse quality.
- Mother nature (environment ): What influence does the environment have? Consider place, time, season, temperature, culture, work ethics et cetera.
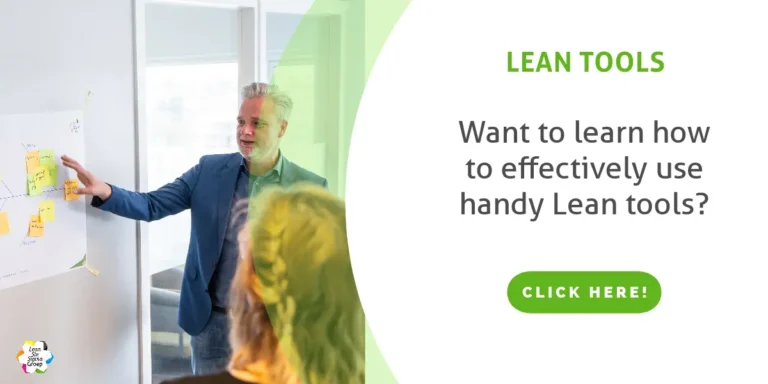
Making the fishbone diagram yourself
- With the diagram, you can easily summarize a cause analysis.
- This cause analysis tool is considered one of the seven basic quality tools in the analysis phase of DMAIC.
- The fishbone diagram identifies many possible causes for an effect or problem.
- It can be used to structure a brainstorming session.
- It instantly sorts ideas into useful categories.