The 5 basisprinciples of Lean Management
The foundation of LeanWhat is Lean Managment?
Lean Management (Lean philosophy) focuses on managing process improvements. It is widely used nowadays in combination with Six Sigma.
Instead of trying to maintain total control over the work processes, Lean management encourages shared responsibility and shared leadership. Therefore, the two main pillars of the Lean methodology are:
- Respect for people
- Continuous improvements
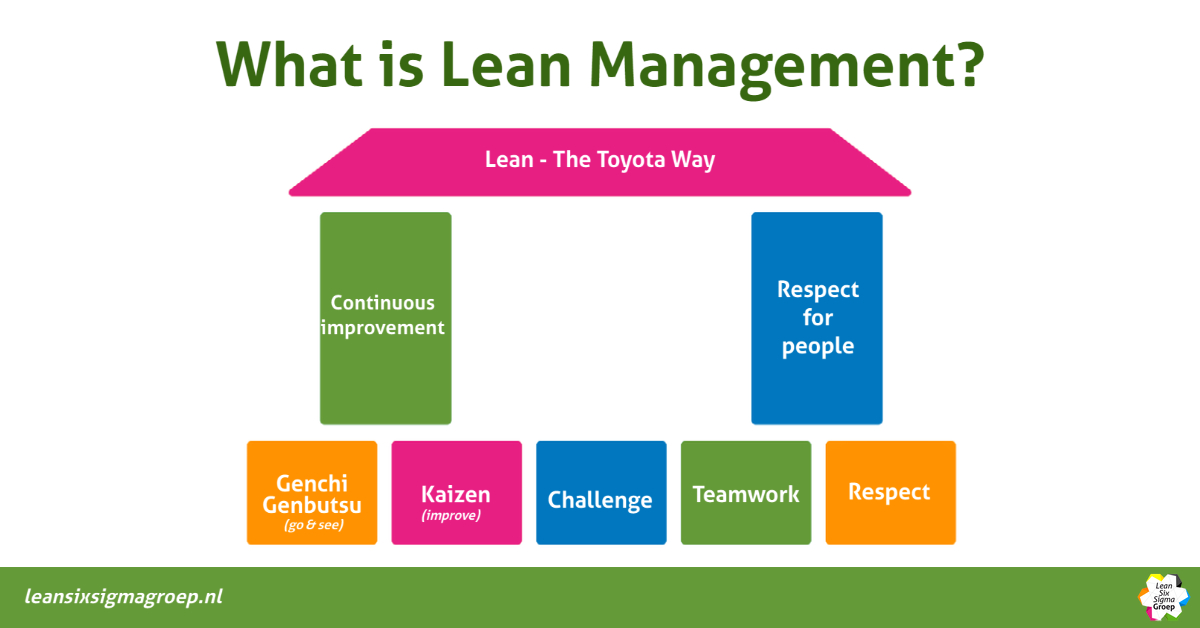
Lean management is currently a concept that is widely applied in various industries. However, it is derived from the Toyota production system, wich was founded about 70 years ago. Lean management is based on 5 basic principles. These principles help to set up processes smartly, help continuously imporve and support in eliminating waste.
The 5 basisprinciples of Lean Management are:
1. Who is the customer of the process and what does the customer want?
The most important basic principle. Who is the customer/who are the customers and what is the added value for the customer? First, think about this carefully, and practice this well. The customer is central to this.
For example, this practice is already possible if you look at a process such as the maintenance of your car: why do you (customer) do this and what is the added value? At the end of the day, you want to drive a car that is well maintained because you don’t want to end up on the side of the road. And because you need an MOT approved car.
Before you go into the process, it is very important to have this sharp. Do you deliver the added value or not? What exactly does the customer think is important with regard to your services or your product?
2. Map the process well
By properly mapping the existing process, it becomes clear how the added value is created and what important steps are to do so. Adding value is central to this.
You also see waste in the process as waiting times, extra steps that are not necessary etc. People often say about their own processes that things are going well but when you map the process well you see the wastes.
A good way to map the process is to create a “Value Flow Analysis” that often uses a piece of paper and post-its.
When maintaining a car, for example, you see that you first have to make an appointment, then drive to the garage, then wait or get a loan car, then pick up the car, pay the bill and drive away. The garage also has a process, you can also map this.
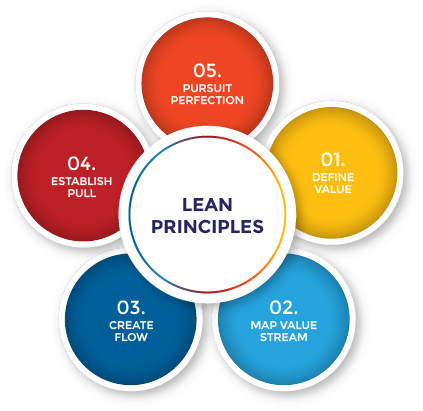
3. How can you bring the flow into the process
This means that you get as much waste out of the process as possible, such as defects and waiting times. This way you keep the steps about delivering added value for the customer.
It is impossible to remove all waste from the process, but often you do this step by step, aiming for a process without waste. If you do this, make sure you are not hindered by what seems impossible.
When maintaining the car, it would be perfect if you don’t have to do anything at all to be able to drive a well-maintained car. So for the garage, it might be an idea to pick up your car and bring it back. Lexus, for example, does this.
4. Think carefully about when do you do something, the so-called pull
How can you set up the process so that it starts when the customer asks for it and then delivers exactly on time, when the customer wants it. It helps to have a process with little waste, so you can deliver quickly.
Pull in production means producing on customer demand. Pull in services means using customer demand to pull the service through the process.
5. Streven naar perfectie
This means that you continuously look at how you can improve further and which step will be next in the daily process. When you have improved, you will carry out the process.
It is nice to get a day or week start here, for example, or in Agile terms a Daily Standup. This way you discuss with each other what is going on, who is doing what and where further improvement is possible.
Lean’s focus is on processes and improving them. In addition, at Lean management you can also see that the vision of the organization is important. Where do you want to go as an organization and how do you get there?
Do you want the above information in a handy clear infographic? Click here
Lean Management in beeld
In the video below, 4 principles of Lean Management will be explained visually. Learn more about Lean Management Principles and how they can help your business eliminate waste and create value for your customers.