What is Six Sigma?
Increase efficiency and effectivenessSix Sigma is a method to increase the efficiency and effectiveness of a process, ie doing the right things and doing things right. The purpose of the method is to reduce variation in processes to meet customer specifications for the product or service.
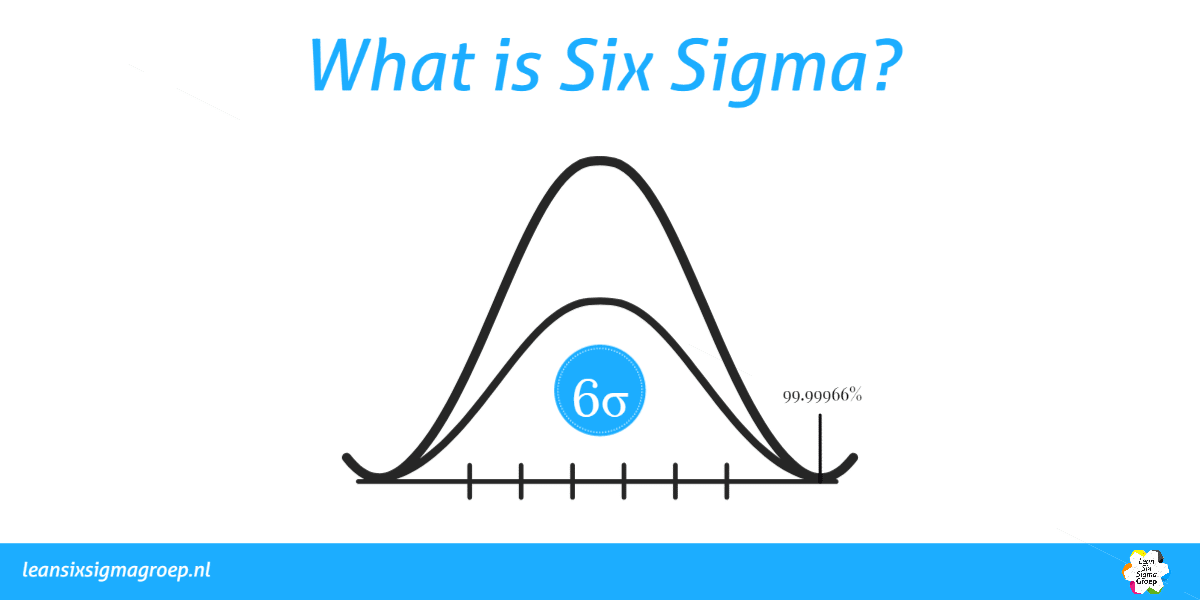
What are the main principles?
- Starts and ends with the customer
- Viewed differently – “every task is a process”
- Process oriented – “limit island culture”
- Eliminate defects – “variation is the enemy”
- Fact-based and data-based decisions – “show me the data”
- Financial results as a starting point
What is the Six Sigma Methodology? – 5 phases of DMAIC
The method consists of five phases, also known as the DMAIC method:
D = Definition phase, this first phase describes the problem we are working on and the value for the company. The customer’s wishes are visualized.
M = Measurement phase, in this phase we measure against the process, we collect basic information about the process / product and we determine the improvement goals.
A = Analysis phase, in this phase you determine the main causes, those are the process factors that have the most influence on the process output.
I = Improvement phase, we determine the best options for improving process performance and we test these solutions.
C = Control phase, the best solution is implemented and the project and new working methods are secured and transferred.
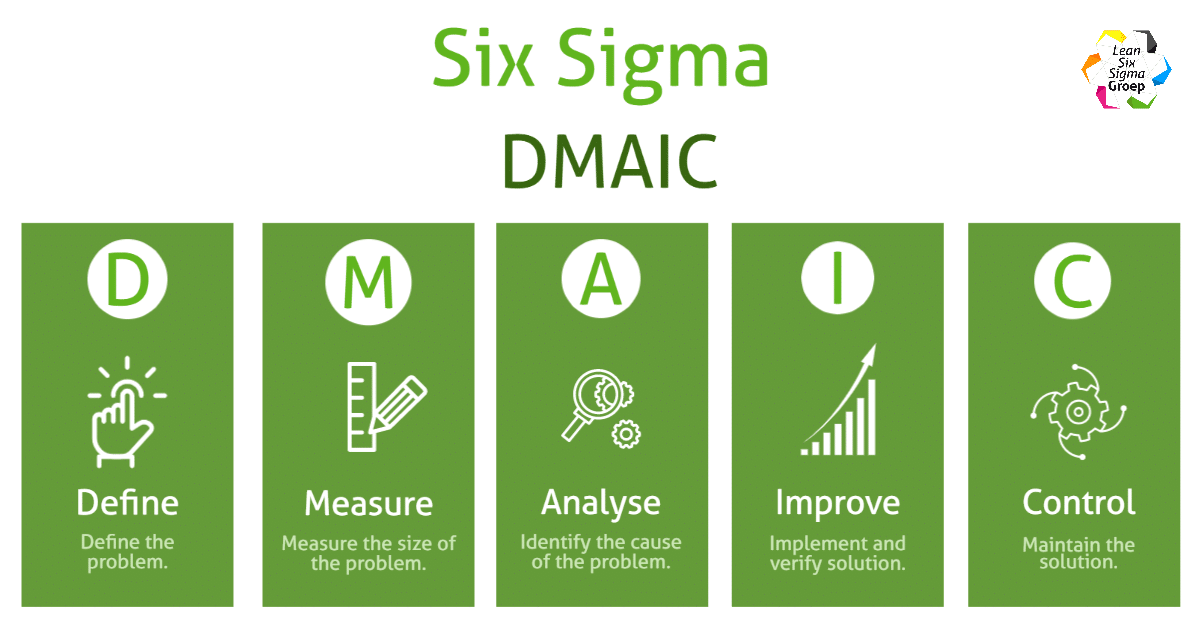
Why Six Sigma?
Sigma stands for standard deviation in statistics, which is the average deviation from the average. Sigma (σ) is the Greek letter that represents the distribution of a distribution. It says something about the distribution of the outcome of your process.
The term comes from the manufacturing industry. A production process can be described with a sigma assessment, which indicates how well a process is performing. The higher the sigma value, the better your process performs. A six sigma process means that there are 3.4 defects on 1 million products. It is a set of techniques and tools for process improvement.
It was introduced by the American engineer Bill Smith while working at Motorola in 1980. Jack Welch made it central to his business strategy at General Electric in 1995. They set Six Sigma as a target for their production processes and developed the DMAIC method described above. . The method has been very successfully applied and spread by General Electric. Six Sigma is not only applicable in industry, but also in business services, logistics, (semi) government and healthcare; actually in every industry.
Implementation roles
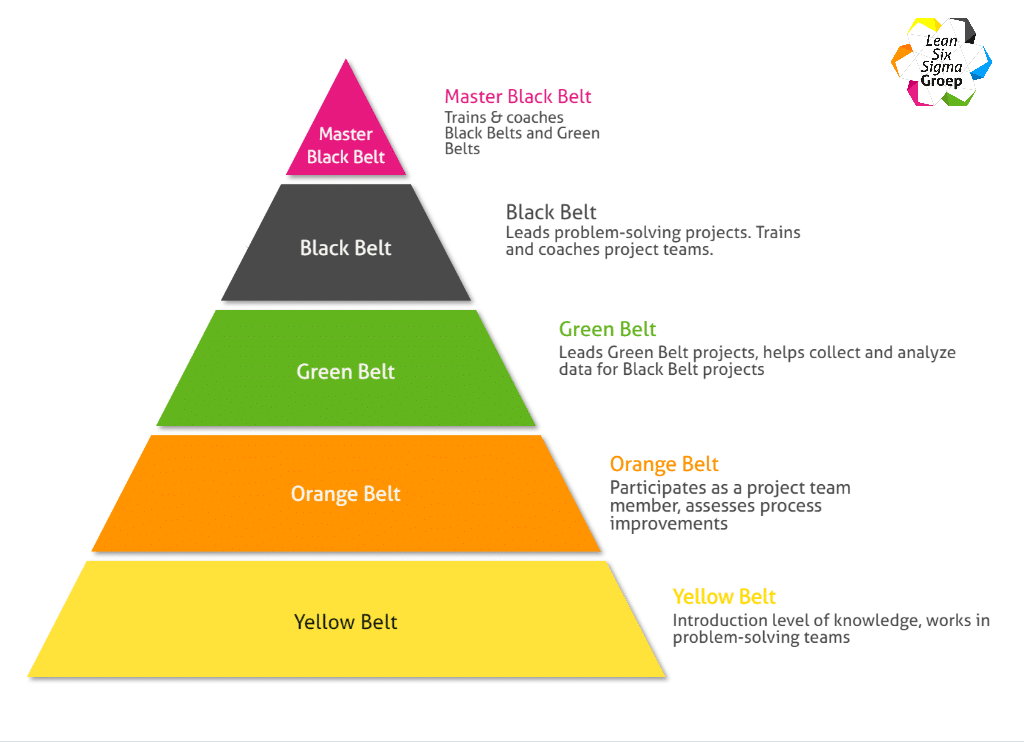
An important innovation concerns the absolute “professionalization” of quality management functions. Prior to Six Sigma, in practice, quality management had been largely relegated to the production floor and to statisticians in a separate quality department. Formal Six Sigma programs use some sort of top position terminology (similar to some martial arts systems, such as judo) to define a hierarchy (and special career path) that encompasses all business functions and levels. The method identifies several key roles for successful implementation.
- Master Black Belts, identified by Champions, act as internal coaches on Six Sigma. They spend 100% of their time on Six Sigma. They help Champions and guide Black Belts and Green Belts. In addition to statistical tasks, they spend their time on the consistent application of Six Sigma across various functions and departments.
- Black Belts work under Master Black Belts to apply Six Sigma methodology to specific projects. They spend 100% of their valued time on Six Sigma. They mainly focus on Six Sigma project execution and special leadership with special tasks, while Champions and Master Black Belts focus on identifying projects / functions for Six Sigma.
- Green Belts are the employees who undertake the Six Sigma implementation along with their other duties and who work under the guidance of Black Belts. According to proponents of the system, special training is needed for all of these practitioners to ensure they follow the methodology and use the data-driven approach correctly.
Some organizations use additional belt colors, such as Orange Belts, for employees who have basic training in Six Sigma tools and generally participate in projects and “White belts” for those trained locally in the concepts but not participating in the project team.
Difference Lean and Six Sigma
Lean focuses on eliminating waste and creating flow in a process. Six Sigma focuses on reducing dispersion within a process.
Lean | Six Sigma |
Focus on process speed | Emphasis on eliminating defects |
Reduction of waiting time | Reducing variation |
Focus on value adding activities | Using statistics, focus on quality |
Tools to handle complexity | Tools for troubleshooting |
Reduce the cost of complexity | Data-driven decisions |
Building an infrastructure for a smooth process flow (flow) | Builds an infrastructure to get and keep results |
Mainly works on efficiency | Mainly works on effectiveness |
Problems usually measured in time (sec.) | Problems usually measured in “pieces” |
Integration of Lean en Six Sigma
Lean and Six Sigma are usually mentioned in the same breath. Both methods strive to meet the customer’s wishes as best as possible. Lean focuses more on process, Six Sigma focuses on the product. Tools from Lean can be used very well with the Six Sigma method, so that the methods fit together well. Lean Six Sigma is a complementary method.