What is a Value Stream Map?
A Value Stream Map is a data-rich process map. The product flow, the process flow, is made visible and supplemented with data and other relevant information. The VSM provides an overview of how a product flows through the process to the customer, it provides insight into the waste and unnecessary process steps.
Meaning
The translation ‘value stream’ can be misleading. The VSM contains all process steps, including those of which it later appears that this step does not add value to the product.
Features of the Value Stream Map
- A VSM is set up from RIGHT to LEFT. Starting with the customer; with the final product that the customer receives.
- A VSM is always drawn up with the employees working in the process.
- A VSM is often made on brown paper (from a roll). All information is written on post-its and pasted on the sheet of paper. Adjusting the process is done in the most convenient way.
Method to set up VSM
First of all, you decide which process you want to take a closer look at. Which process is not going well and needs to be improved?
A VSM is built in a number of steps:
- Start with the customer. Determine who the customer is and what he wants. How many products does the customer want to receive, when and in what way?
- Name the main suppliers. How often is delivered, what is delivered and how?
- Draw the process steps starting with the last one, which is the customer. Always ask the question: ‘Who did he/she get this from?’. Briefly describe the process steps.
- Collect relevant data during the process steps in a data box. eg. processtime, cycletime, how many failures per process step.
- Collect additional information about the flow of the process, such as how much stock and how long it is waiting, how long does the process step take.
The current process has now been mapped, this is called the current state. This is the routing a product is following at the moment. It is a visual representation of the process including material and information flows. Sources of waste are shown, such as stock and waiting time.
The places of waste are places where, after a good analysis, improvements can be made.
You then map out the ideal VSM. One where the product flows through the process without waste. This is called the future state of the VSM.
This is followed by the preparation and implementation of an improvement plan to arrive at the future state of the VSM.
Benefits of a Value Stream Map
All employees in the process have the same overview of the process. It has become a collaborative process. Together, the step towards an improved process can now be taken.
Example of a Value Stream Map
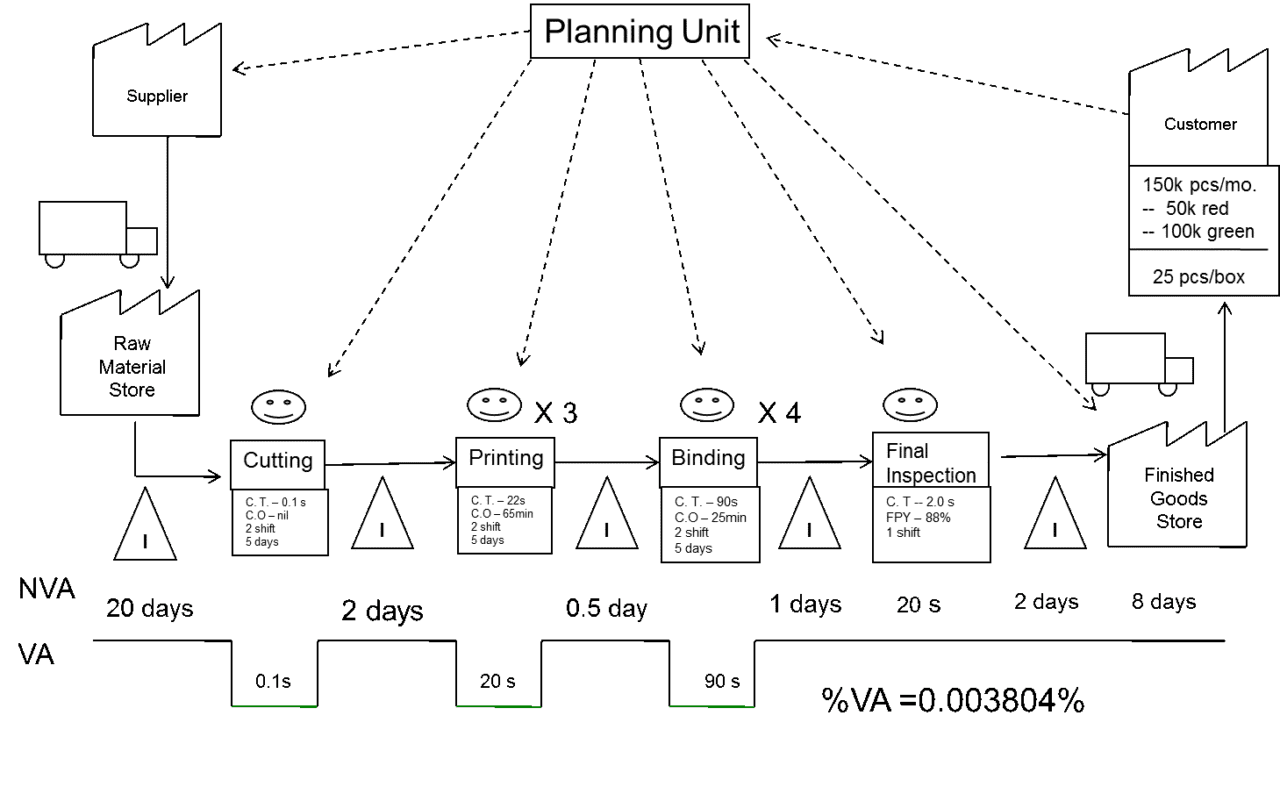